As a specialist in industrial simulations, eCon Engineering Kft. contributes to the development of aircraft. The Virtual Blade Model, developed with funding from the National Research, Development and Innovation Fund, could bring a quantum leap in the aerospace industry: the application of artificial intelligence not only makes structural analysis, aerodynamic calculations and tests required during manufacturing more accurate and cost-effective, but also radically speeds up the process.
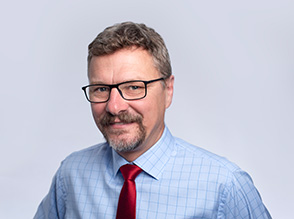
Gábor Kiglics, Managing Director
eCon Engineering Kft.
Founded in 2002, the Hungarian company has more than two decades of experience in engineering simulation, virtual prototyping and automation. The aerospace and composites industries represent a promising market and dynamic growth opportunities for the company in the future. Speed, high quality and cost-efficiency are vital in these industries (too), which is why market operators demand these types of high added-value services that can give them a tangible competitive advantage.
eCon has collaborated with aircraft manufacturer Altus Aero on the development of a new type of light aircraft. Their project has resulted in the Virtual Blade Modell, an innovative combination of artificial intelligence and statistical methods that can simulate propeller-induced flow around an aircraft body more accurately and efficiently than simplified two-dimensional or complex explicit three-dimensional flow analyses. The process allows the effects of the propeller on the airframe structure to be mapped quickly and comprehensively, and the data can then be used to optimise development and production. The results obtained from virtual simulations have been successfully confirmed by real flight measurements. Following more than three years of design and construction, the Altus prototype took off for the first time in June 2018 and has now flown almost 1,000 hours, performing as well in cold alpine weather as it does in hot coastal or rainy environments.
All this shows that the Virtual Propeller Model simulation procedure developed is indeed a reliable tool for solving an industrial problem, and thus can be used as a marketable service in the future. Moreover, parameter calibration through optimization methods is giving rise to a new set of procedures that are being developed.
The procedures developed offer significant efficiency gains in the engineering processes, which can be applied not only to the light aircraft covered by the project, but also to rotorcraft, rotary wing applications, structures, be it wind turbines, rotorcraft, etc.
The project has clearly led to the implementation of additional industrial projects, significantly enhancing the development of the national engineering and technical ecosystem and the retention of the engineering community in the region.
(Project code: 2018-1.1.2-KFI-2018-00057)
registered office: 1116 Budapest, Kondorosi út 3.
Consortium partner: Infominero Kft.
Number of employees: 97
Of which research and development engineers: 14
Net turnover: HUF 3,167,804,000
Export turnover: HUF 761,915,000
University collaboration: Department of Fluid Mechanics, Budapest University of Technology and Economics