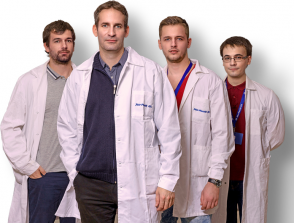
Ferenc Ronkay and his project team
In Hungary approximately a hundred thousand tons of PET-raw material (PET: polyethylene-terephthalate) is used for manufacturing plastic bottles. They very soon become waste: virtually all the amount ends up in rubbish bins already in the year of manufacturing. Earlier this type of waste was exported abroad, primarily to the Far-East, where it was used in the textile industry as raw material for polyester. Nowadays, an increasing amount of PET-waste is processed also in Hungary. Usually, they are used to make packaging materials from for the food industry, but this is only possible in the case of “water pure” and blue bottles. As the properties of coloured bottles are as good as those of transparent ones, the researchers working at the Department of Polymer Engineering of the Budapest University of Technology and Economics came up with the idea of colouring the waste bottles of different colours black, which will make them suitable for being reused as technical products. Of course, before that certain properties of the raw material need to be modified, e.g. its mechanical strength increased or flammability reduced. Therefore, the main objective of the research funded from the NRDI Fund is to use PET as a raw material to develop composites whose upgraded properties (e.g. increased mechanical properties, flame retardancy) make them more valuable, more convenient for being used in a number of areas, and more cost-effective to produce.
Primarily, the project aimed to find new fields of application in the electronic or automotive industry. Ferenc Ronkay, the project leader said: “Compared to other types of plastic, PET is less flammable, this was a good basis to start from. Our main objective was to develop a product of the best possible quality by using as little flame retardant agents as possible. A large amount of flame retardant agents will make its mechanical properties deteriorate - you can’t improve all the properties at the same time. We enhanced flame retardant agents with various synergistic nano-additives, which helped us reduce the proportion of additives to 6-8%. This is already something that industry has also shown interest in.”
„Industrial application is so close to my heart that I’ve decided to accompany the project and continue work in industry myself, now I work for Jász-Plasztik Kft., one of the largest companies in plastic processing - said Ferenc Ronkay. – This company has set up a development laboratory, where I try and put the findings of the project into practice. For the developments to achieve their objectives, industrial experience is indispensable.”
The processing of waste PET bottles comprises the following stages: bottles are collected, then baled. In the plant they are unbaled, then shredded. Shredded material is purified, but it also needs to be sorted and separated from non-PET-based waste, such as caps. Those working on the project developed a sorting machine for this purpose, with a centrifuge as its major component. Centrifuges have long been in use to separate various materials, but separation of plastic in melted state has been a novel use. For this purpose a prototype was made: the plastic mass is heated up, melted then rotated in the centrifuge. Various types of plastic with various density are separated in individual layers. This is the efficient method of separating waste.
![]() |
![]() |
The prototype of the melt centrifuge and a 4-component plastic compound after separation |
Jász-Plasztik Kft. uses purified PET bottles to manufacture transparent egg boxes from, but they have also had the idea of producing foam structured boxes (which currently are made of polystyrene). Under laboratory circumstances they have already managed to foam plates, however, its industrial application takes some more work. Previously they experimented with gas-generating additives and supercritical carbon-dioxide, as well. Under a sufficiently high pressure and at a sufficiently high temperature carbon dioxide becomes fluid, this needs to be dispersed in the plastic melt. When the melt gets into the processing equipment, carbon dioxide due to the lower pressure will convert back into gas, which will be locked in bubble cells inside the material.
![]() |
CT-image of recycled PET-products die-cast with various foaming agents |
![]() |
![]() |
Flame retardant electronic cover made of recycled PET and typical heat emission curves |
“We have been making good progress introducing flame retardant, recycled PET bottles - continued Ferenc Ronkay. As regards the components of electronic appliances of a larger size, e.g. the backplates of TV sets, there are strict flammability requirements to observe. Products are often made of polycarbonates (PC) and its further blends, but these contain two or three times more flame retardant additives than the amount we put into PET, which significantly drives up production costs. Consequently, PET would be an excellent raw material to replace polycarbonates, mostly PET recycled from waste: it can be coloured nice, glossy black, it has very good mechanical properties, it’s durable and based on our formula it is also competitive with other plastic types used for the same purpose in terms of flammability parameters. PET-waste of different colours is cheap, because they are processed by only a few, and due to the reduction of the amount of flame retardant additives, we have managed to produce a genuinely marketable product.”