A gyártás során a termékek előállítása csak a folyamat első lépése. Legalább ilyen fontos az elkészült gyártmány minőségének ellenőrzése, hiszen a hibák miatt nemcsak hatalmas veszteségei adódhatnak a cégnek, de például a járműiparban akár emberéletek is múlhatnak rajta. Ezért rendkívüli jelentőséggel bíz a mind megbízhatóbb, sokoldalúbb ellenőrző módszerek, gépek üzembe állítása. Ilyen univerzálisan használható ellenőrzőberendezés kifejlesztését célozza a BaseClass Automation Kft. projektje, amellyel a cég az NKFI Hivatal által folyósított A Vállalatok K+F+I tevékenységének támogatása (VÁLLALATI KFI_16) című pályázati felhívás keretében nyert el majdnem 136 millió forintos támogatást.
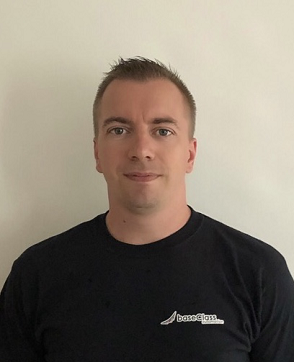
Gaudia Andor, a BaseClass Automation ügyvezető igazgatója
A „Vállalatok K+F+I tevékenységének támogatása” című felhívás a tudásintenzív, innovatív vállalkozásokat ösztönzi jelentős szellemi hozzáadott értéket tartalmazó, új, piacképes termékek, szolgáltatások, technológiák házon belüli kifejlesztésére. A konstrukció keretében közép-magyarországi mikro-, kis- és középvállalkozások, valamint nagyvállalatok igényelhetnek 80–500 millió forint közötti forrást, a Nemzeti Intelligens Szakosodási Stratégiában meghatározott ágazati prioritások valamelyikéhez illeszkedve, önállóan vagy konzorciumi együttműködésben végzett kutatás-fejlesztési és innovációs tevékenységük finanszírozására.
A BaseClass Automation Kft. alapításakor, 2012-ben a gyártástechnológia számos szakágával foglalkozott a szoftvertervezéstől a géptervezésen és -gyártáson keresztül az automatizálásig, robottechnikáig. Később aztán már egyre inkább az automatizálási szakirányra koncentráltak.
„Egyedi gépeket terveztünk, gyártottunk és üzemeltünk be, főként magyarországi multinacionális vállalatok megrendelései alapján – válaszolja kérdésünkre Gaudia Andor, a BaseClass Automation ügyvezető igazgatója. – Leginkább autóipari beszállítók részére gyártottunk ellenőrző rendszereket, mérőgépeket, feldolgozó robotokat. Minden gépünk egyedi, szinte nincs is két ugyanolyan, hiszen mindet a megrendelő igényeire szabjuk.”
Miközben e vonalon fejlődött a cég, nemrégiben az egyik megrendelőjükben felmerült egy olyan gép iránti igény, amellyel univerzálisan lehet különféle alkatrészeket ellenőrizni. Ebből a kamerarendszerrel, ipari robottal felszerelt gépből hármat meg is építettek, amelyek mind a mai napig működnek is a megrendelő üzemében. Ugyanakkor a használata igen bonyolult, az irányítónak speciális képzésre van szüksége, a felhasználási területe pedig meglehetősen korlátozott. E tapasztalatokból kiindulva a BaseClass Automation vezetői egy olyan ellenőrző eszköz ötletén kezdtek el gondolkodni, amely univerzálisan használható az autóipari alkatrészek gyártásában, és százszázalékos ellenőrzést tesz lehetővé.
A gyártástechnológiában az ellenőrzés, a minőségbiztosítás talán a végtermék megbízhatósága szempontjából a legfontosabb fázis. Ha az alkatrész soklépcsős gyártása bármely állomásán hiba történik, és ezt a hibát nem fedezik fel azonnal, akkor a hiba nagy valószínűséggel csak sokkal később fog kiderülni. Akár akkor, amikor az alkatrészt már beépítették a nagyobb gépezetbe, például egy autóba, akár még később, amikor a vevők már használják, esetleg amikor az alkatrész hibájából kifolyólag már működési probléma keletkezett.
Érthető, hogy a gyártónak annál több költséget, veszteséget okoz a hiba kijavítása, minél később veszik észre. Ezért van elsőrendű jelentősége a „valós idejű” és százszázalékos, tehát minden egyes legyártott munkadarabot érintő ellenőrzésnek. Ez azonban a gyakorlatban gyakran nehezen megvalósítható, illetve nem gazdaságos. Vannak például olyan kis szériában gyártott alkatrészek, amelyek ellenőrzésére nem éri meg egy – e feladaton kívül semmi másra nem használható – célgépet beállítani. Ilyenkor általában szúrópróbaszerűen ellenőriznek. Ha pedig eltérést tapasztalnak, leállítják az egész gyártási folyamatot, és akár egy egész műszak során gyártott alkatrészeket is ki kell dobniuk.
„Azok a berendezések a célszerűek, amelyek minden egyes darabot ellenőriznek, és regisztrálják az ellenőrzés tényét. Így biztosak lehetünk abban, hogy az adott fázisban nem történt hiba. E gondolatból született meg a Redbox nevű berendezés ötlete, amelyet az elnyert támogatás segítségével fejlesztünk – folytatja Gaudia Andor. – A most épülő gép számos előnyt egyesít magában: úgy működik, mint a koordinátamérő gépek, viszont gyors, az összes munkadarabot képes megvizsgálni, és nem igényel klimatizált helyiséget a működéséhez.”
Maga az ellenőrzés is komplex folyamat. E modern monitorozóberendezések már gyakorlatilag a termék minden olyan tulajdonságát meg tudják vizsgálni, amelyet egy emberi minőségellenőr is megnézne. Távolságot mérnek tapintással vagy optikai elven (kamerákkal és lézeres távolságmérők segítségével). A kamerák képeit elemezve meg tudják állapítani, hogy minden alkatrész a helyén van-e, a méretek megfelelőek-e, ott van-e a furat, a bemarás, ahol lennie kell, és így tovább.
A Redbox optikai elven, érintés nélkül fog mérni, a mérőberendezéseket pedig egy öttengelyes robot mozgatja majd. A munkadarab szállítópályán érkezik és megy is tovább. A felszerelt kamerák rendkívül gyorsan működnek, másodpercenként akár öt képet is készíthetnek. A termék mérési eredményeit a sorozatszáma alapján akár évekkel később is elő lehet hívni az adatbázisból, ami adott esetben akár a balesetek okainak felderítését is szolgálhatja.